As consumers across the globe become more digitally dependant, modern businesses are being forced to increase energy consumption to meet the demands of online business operations and data storage requirements. A key issue facing businesses is the risk of unplanned downtime, which can have a potentially devastating impact on both profitability and brand reputation.
Reduced levels of reliability found in older low voltage switchgear assemblies puts continuity of service at risk. Therefore, it is vital that facility managers have an appropriate life extension strategy in place to manage this risk. Both maintenance and modernisation play a key role in low voltage switchgear life extension.
Maintenance
The two most effective forms of maintenance for ensuring continuity of service are predictive and preventive. Whilst distinctly deferent in approach, each form is complementary to the other when combined within one singular life extension strategy.
- Predictive Maintenance
Predictive maintenance ensures the quality of the end users power supply by monitoring equipment overtime to predict any impending failures. System alerts can be triggered to notify the end user of potential issues so the appropriate corrective actions can be taken.
- Preventive Maintenance
Preventive maintenance involves regular testing and inspection of the switchgear components to identify and rectify issues that may increase the likelihood of switchgear failure. Maintenance can be scheduled based on a time or usage trigger. Planned maintenance typically costs less than reactive maintenance as it can be scheduled to coincide with periods of low activity, reducing disruption to business operations.

By following the steps below switch room managers can extend the useful life of their low voltage switchgear assemblies whilst avoiding costly unplanned downtime.
- Visual Inspection
A visual inspection should be carried out throughout each stage of maintenance to check for the build-up of dust or debris. It also important to assess the tightness of connections and discoloration of parts which may point to a greater issue.
- Cleansing and Lubrication
All connections, disconnect switches, racking mechanisms, and interlocks must be thoroughly cleaned and lubricated to ensure fast contact speed. Without adequate cleaning and lubrication, mechanisms can begin to rust resulting in slower operation of critical parts.
- Insulation Testing
As soon as insulation is made it starts to deteriorate with harsh environmental conditions being a key catalyst. As insulation deteriorates reliability becomes reduced, resulting in potentially dangerous operating conditions. Several tests can be carried out to identify points of deterioration in insulating materials such as insulation resistance testing, power factor testing and high-potential (Hi-pot) testing.
- Mechanical Testing
All mechanical interlocks, door locking, and control devices must be inspected for correct operation and sequencing. Many mechanical processes such as remote racking of circuit breakers are set in place to preserve operator safety. Therefore, any degree of maloperation can have potentially fatal consequences.
- Electrical Testing
Low Voltage switchgear is made up of an extensive range of electrical components which control the main system function of carrying, making and breaking the load current and clearing electrical faults. It is important that all electrical components including but not limited to circuit breakers, circuit transformers and protection replays are maintained to ensure efficient switchgear operations.
- Monitoring
Online monitoring systems are a form of predictive maintenance and can be integrated into low voltage switchgear systems to monitor electrical performance. Online monitoring systems provide 24/7 system support, triggering an alert to notify engineers of any impending failures. The main advantage of a monitoring system is that it can identify an issue that may not have materialised or may have been overlooked at the time preventive maintenance was last conducted.
- Thermal Imaging Survey
Thermal imaging can help detect excess heat in electrical components. It can be carried out while the system is under a full load with no impact to operations. Thermal imaging technology can detect loose connections, corroded elements, short circuits, overloaded circuits and busway-joint analysis. This non-invasive technique also allows to gather data from a remote location, away from potentially dangerous situations.
Modernisation
Whilst a structured maintenance plan is vital for low voltage switchgear life extension, older systems can often run into issues with availability of spare parts, insufficient fault limits or compatibility with new standards and technologies which simply cannot be resolved through maintenance. Therefore, it is important that throughout its life cycle, switchgear is not only maintained but also modernised to avoid issues that may put continuity of service at risk.
Switchgear modernisation, often to referred to as ‘retrofitting’ consists of specific components being completely removed from the enclosure and replaced to enhance system performance. There are two approaches to retrofitting, both of which aim to improve power reliability and reduce life cycle costs.
- Direct replacement
This approach involves fitting a new component into the existing switchgear compartment. An adapter cradle can be used to make newer components compatible with the existing switchgear assembly. As no additional modification to the switchgear assembly is required, the replacement can be completed in a short time frame, reducing downtime to a minimum.
- Retrofill
This approach involves modernising the switchgear assembly by carrying out modifications to the component cubicle and bus to facilitate compatibility with the new replacement component. As the assembly has been modified to accommodate the new component an adapter cradle is not required. Modernising switchgear assemblies by retrofilling components allows for greater life extension as the assembly will be compatible with newer more efficient technologies with potentially better interrupting and protection properties. However, due to the additional modification work retrofilling is a typically much lengthier process than direct replacement, requiring a significant amount of downtime to complete.
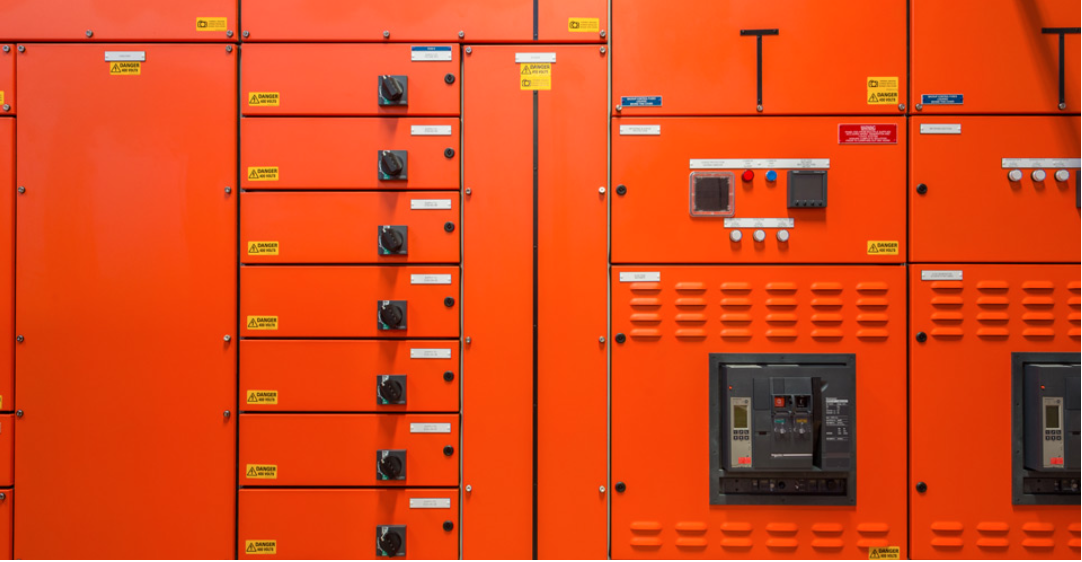